When the package is the size of a dresser
In the furniture industry, where products are large, have various shapes and are often of high value, appropriate packaging plays an important role in the logistics process.
On a daily basis, we work with many companies that produce various types of furniture – from smaller items such as chairs or small tables to armchairs, wardrobes and large lounge sets. The wider the range, the more difficult it is to unify the packaging system. This is especially true since the materials from which the products are made require different types of protection.
Does this mean we are doomed to chaos, many different packages and a stuffy warehouse? Nothing could be further from the truth.
Although this is a challenge, all it takes is a good analysis of the process, selection of appropriate packaging materials, e.g. dedicated to a given company (dimensions, thickness, perforation) and standardization of work in the warehouse to optimize packaging costs and time. In the post below, we’ll show you how you can do this in your company.
Packaging Challenges in the Furniture Industry
The clients we work with came to us with various challenges, which largely depended on the standards of work in the warehouse, the type of assortment and the packaging system adopted. A few key ones are:
- Standardization of packaging of furniture of different sizes and shapes.
- Elimination of damage, e.g. scratches on painted fronts or imprinted bubbles from bubble wrap on materials such as velvet & velour.
- Reducing the number of types of packaging materials (optimizing the buyer's working time and freeing up space in the warehouse stock).
- Using a homogeneous product (recyclable).
- Flexible planning with the supplier of production and supply of packaging materials to reduce warehouse stocking while avoiding shortages of key products.
- Matching the quality of packaging materials to the quality of the product (not every company produces furniture for tens of thousands of zlotys and then it is necessary to find compromises on the quality vs. price line).
- Speeding up packaging times and making the work of warehouse workers easier.
Each of these challenges requires time to analyse and test different products, but each time, working with the buyer and the head of warehouse logistics, we came up with solutions that significantly impacted the efficiency of the packaging process.
Types of furniture damage caused by packaging errors
Improper packaging of furniture can lead to various damages that reduce its value and aesthetics, as well as generate additional costs related to complaints and product replacement. Below we present the most common types of damage resulting from improper selection of packaging materials or errors in the packaging process itself, which our clients faced when contacting us with a request for a quote, as well as the solutions we applied in each of the cases.
Scratches on the painted fronts are caused by cardboard which produces a lot of dust.
SOLUTION: Replacing cardboard with polyethylene foam. Sometimes you will need foam with a higher density, and sometimes regular foam will be enough - it all depends on the production process of the furniture and how long after varnishing it is packed for shipping. The more hardened the varnish, the greater the chance that regular foam will be sufficient to protect the furniture. The right choice affects the costs, so it is worth testing it thoroughly on a selected batch of furniture.
Imprinted bubbles from bubble wrap on upholstery of sofas and armchairs.
SOLUTION: Some of our clients have stopped using classic bubble wrap as a material directly touching the furniture upholstery and have replaced it with a 3-layer film (smooth film - bubble - smooth film) or laminate (a combination of 3-layer film and foam).
Dents on wooden surfaces caused by insufficient cushioning or too thin protective layers.
SOLUTION: Our clients, wanting to avoid heavy furniture from hitting each other during transport, started protecting its surface with laminate, thicker polyethylene foam or three-layer bubble wrap. The choice depends, of course, on the weight of the furniture and its susceptibility to dents, so the packaging product should be selected individually through quality tests.
Broken corners and chipped edges resulting from lack of adequate protection on the corners of furniture.
SOLUTION: In this case, the solution used by our clients is quite simple – polyethylene profiles matched to the furniture. They perfectly surround the corner parts of furniture and absorb impacts.
Deformation of cushions and other small upholstered elements caused by wrapping them too tightly with stretch film or tape.
SOLUTION: Stretch film is a material that needs to be tightened quite tightly for its use to make sense. In situations where this causes unsightly deformations, items such as cushions can be placed in a polyethylene foam or bubble wrap bag and the ends secured with packing tape. At Mac-Graf, bubble wrap bags can be of any width, and the height for closed bags is up to 90 cm, and for perforated bags up to 170 cm.
Damage to decorative elements, e.g. handles and legs (of sofas, armchairs) due to improper securing.
SOLUTION: Our clients successfully pack smaller furniture items in bubble wrap bags, made to measure. They are then well protected thanks to bubble cushioning, and packaging costs and time are optimized.
Product damage due to improper packaging of self-assembly kits or accessories.
SOLUTION: This is a similar situation to the one above – screws, spacers, mini tools and other self-assembly elements must be well protected so as not to scratch the surface of the furniture. Bubble wrap bags provide better protection than, for example, string bags or classic plastic bags, because the bubbles provide an additional layer of cushioning and are much more difficult to break.
Bags can also be made of polyethylene foam, but the cost should be verified on a specific example, because foam above a certain thickness is more expensive than bubble wrap. However, it may be that it is enough to use less thick PE foam instead of bubble wrap and this will be sufficient protection.
Moisture and dirt getting into furniture boxes from the bottom of the pallet on which the products are transported (particularly severe in autumn and winter).
SOLUTION: One of our clients, who wanted to eliminate this problem, opted for a thicker sheet of polyethylene foam (1-3mm depending on the weight of the load), which the packers place on the pallet before placing the boxes on it. Thanks to this, the load is secured both from the top and the side (stretch) as well as from below. This is a good alternative to cardboard dividers, as it protects the goods better in the event of heavy rainfall and high humidity (it does not get wet).
Test different solutions
Due to the specific nature of the product range and the setting of the packaging process, not every solution will work in every company. For this reason, it is important to test new packaging materials, e.g. on a selected batch of products, before globally implementing the change in the entire warehouse or later – in all distribution centres. It is worth implementing a structured quality test, carried out by production, which will be recorded in a report so that the purchasing department can very reliably evaluate the offer of a specific supplier. Additionally, measuring the packaging time and describing the process step by step will allow for actual verification of the impact of optimization on the business.
It is almost always financially beneficial to reduce the packaging layer. The classic packaging system, quite common in the furniture industry, assumes the following scheme:
This is good, but...
In this area there is the potential to reduce the layers by at least one, which is beneficial not only in terms of the total cost per square meter of packaging materials, but also in limiting one or more warehouse operations (reducing packaging time).
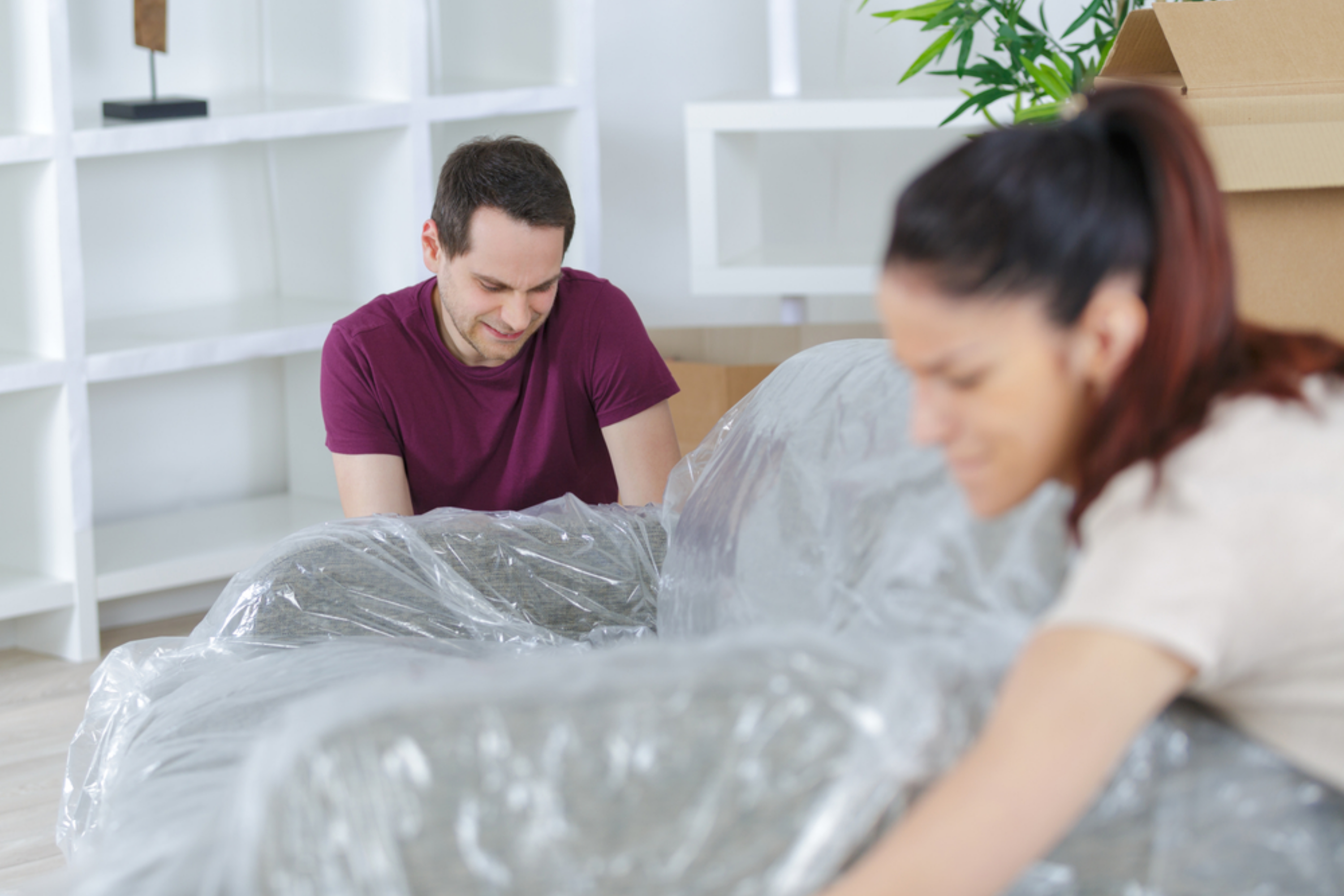
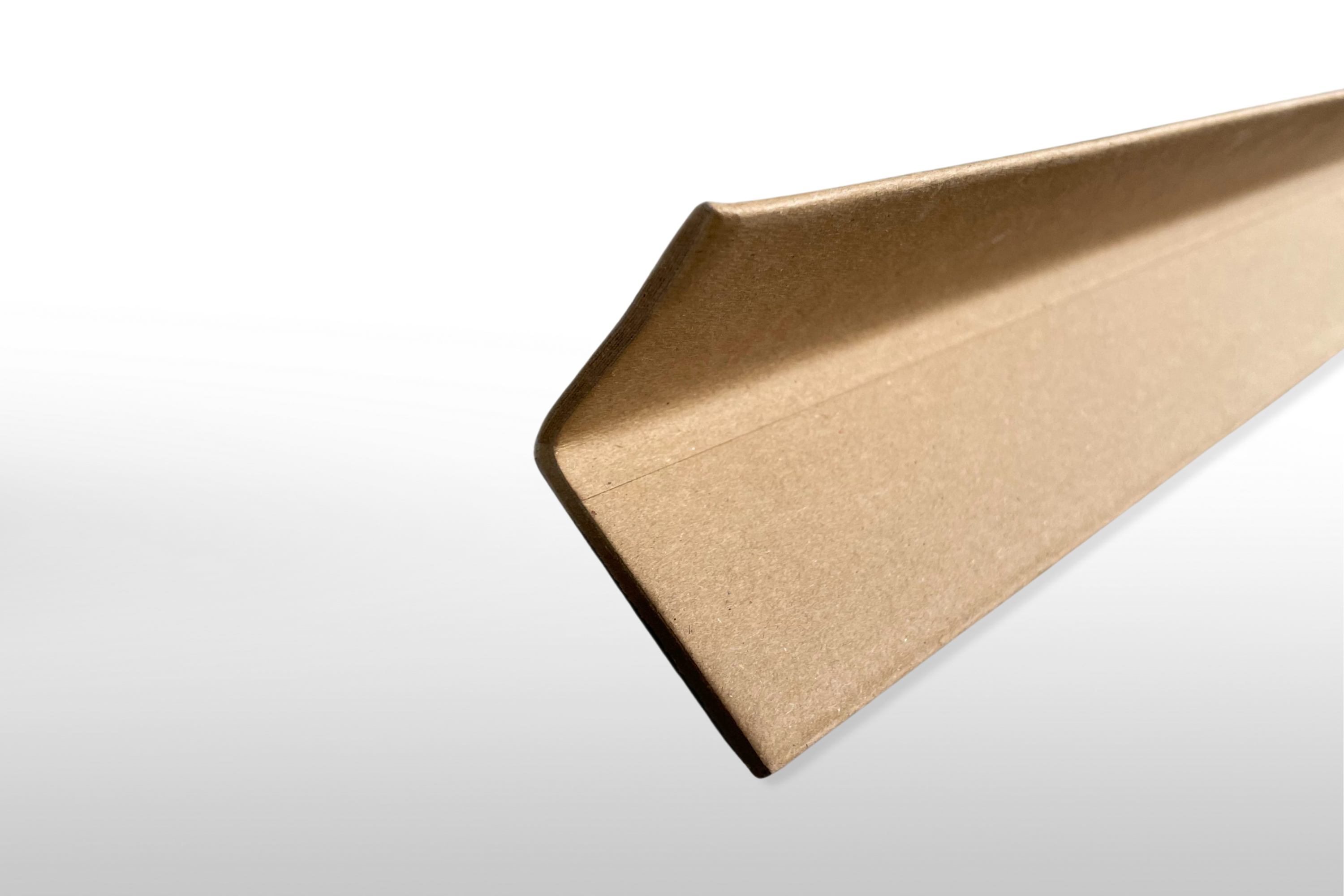
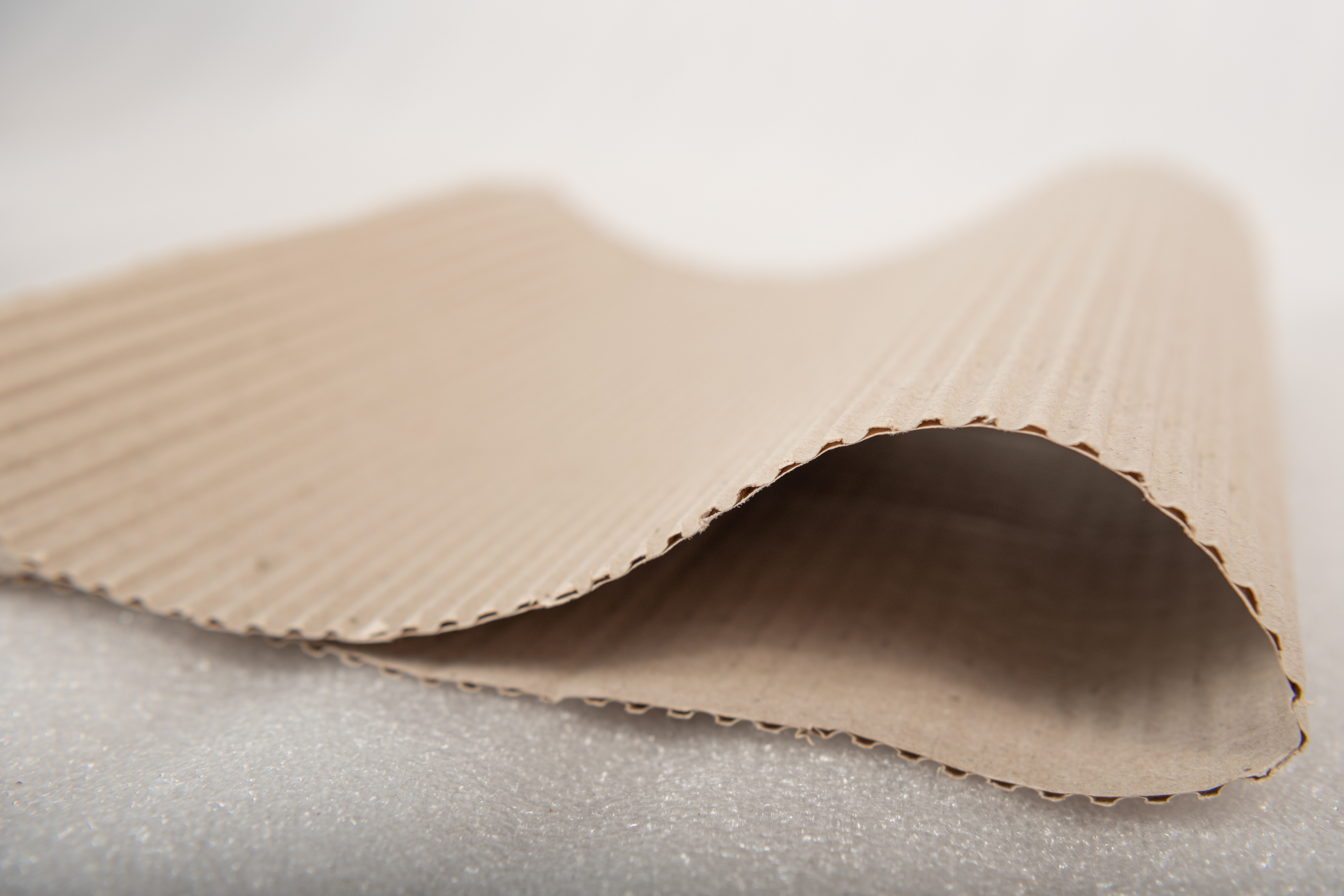
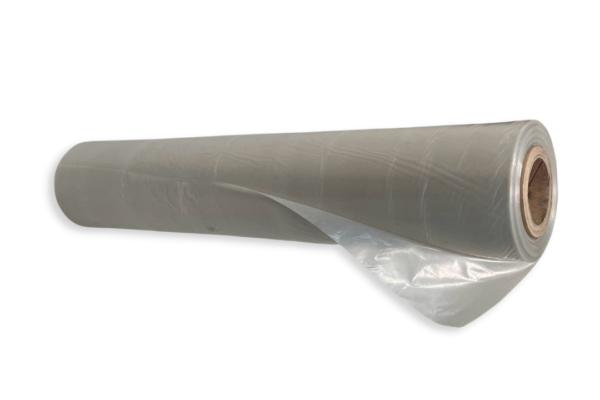
That way is much better and cheaper!
In many cases, taking into account the above scheme, you can successfully replace the dust-proof film and cardboard with a laminate of bubble film and PE foam.
Make recycling easier!
If corners are not used for packaging, this change also means that we use homogeneous materials in terms of recycling.
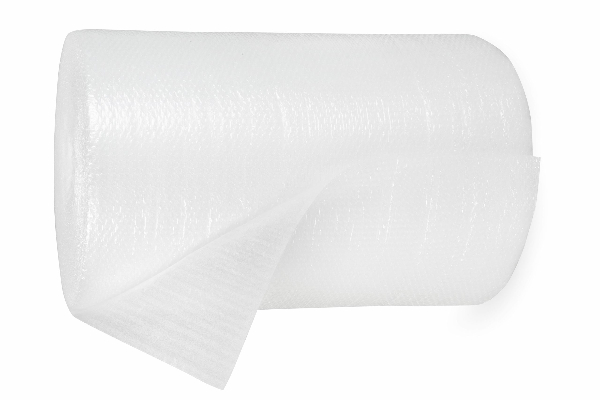
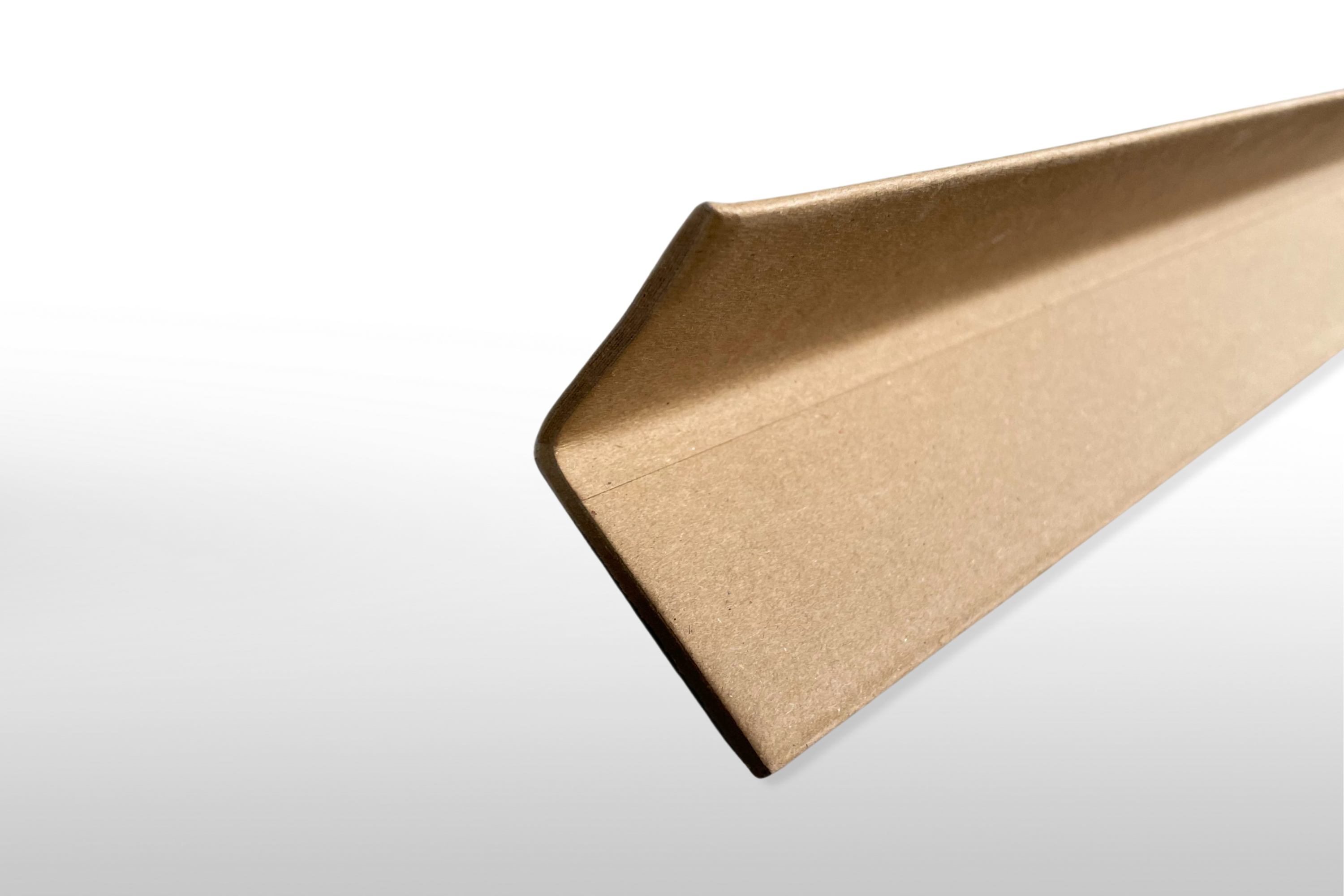
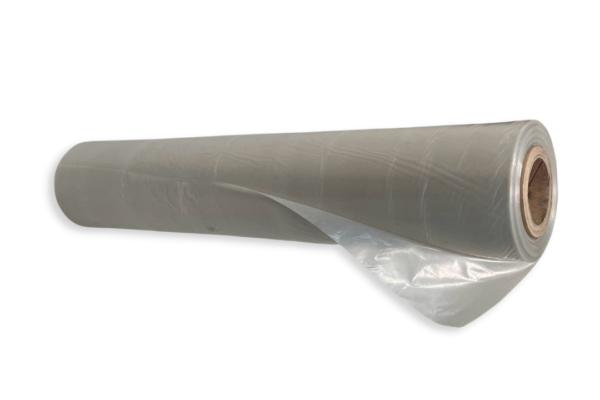
Get an offer from our advisor!
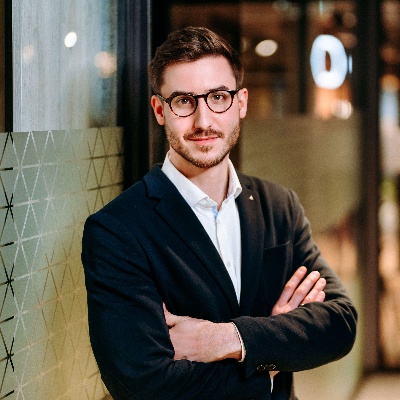
Wojciech Szafranek
Sales Representative
How did we help our clients optimize their furniture packaging system?
While the furniture industry generally follows its own standard rules, each company has its own set of processes, different expectations regarding packaging materials (e.g. recycling requirements) and resources (people, machinery, storage space, budget). For this reason, every time we start working with a client, we try to understand their needs and the way they function and only then, based on our experience, indicate what optimization options might work for them and why. Rarely is it a revolution that turns the entire packaging system upside down. At the beginning we are looking for small improvements that will be quick wins and will allow for quick, real savings of time and money.
We have many stories we could share – they have 30 years of experience behind them. Below we provide three examples of implementations described in more detail:
Case 1 | Replacing two products with one tailored to the company's needs
One of our clients used cardboard and polyethylene film to pack furniture. Using two materials was problematic for several reasons – it increased packaging time, it was necessary to maintain stocks of two different materials, and they were not homogeneous in terms of recycling. We then suggested replacing the two materials used with one – a laminate of bubble wrap and polyethylene foam. Thanks to this, it shortened the packaging time, reduced the warehouse space used for storing packaging materials and, importantly, the material facilitated recycling because it is homogeneous (even though it is a laminate).
The SONG polyethylene foam and bubble wrap we produce, as well as the packaging (sleeves, half-sleeves, bags, sheets) are recyclable at a level of 95-100% (A), which has been confirmed by an independent research institute: Łukasiewicz – Lodz Institute of Technology.
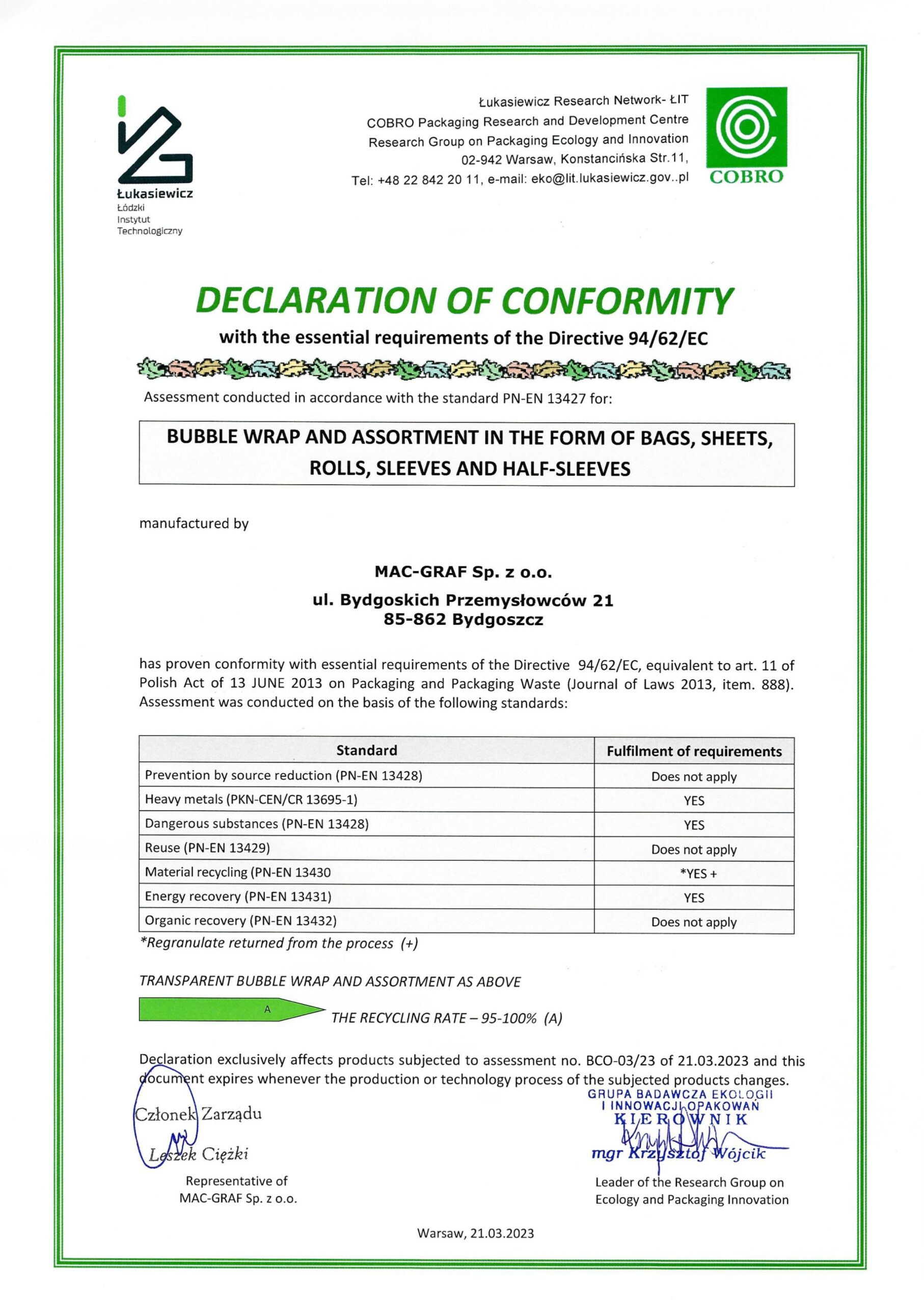
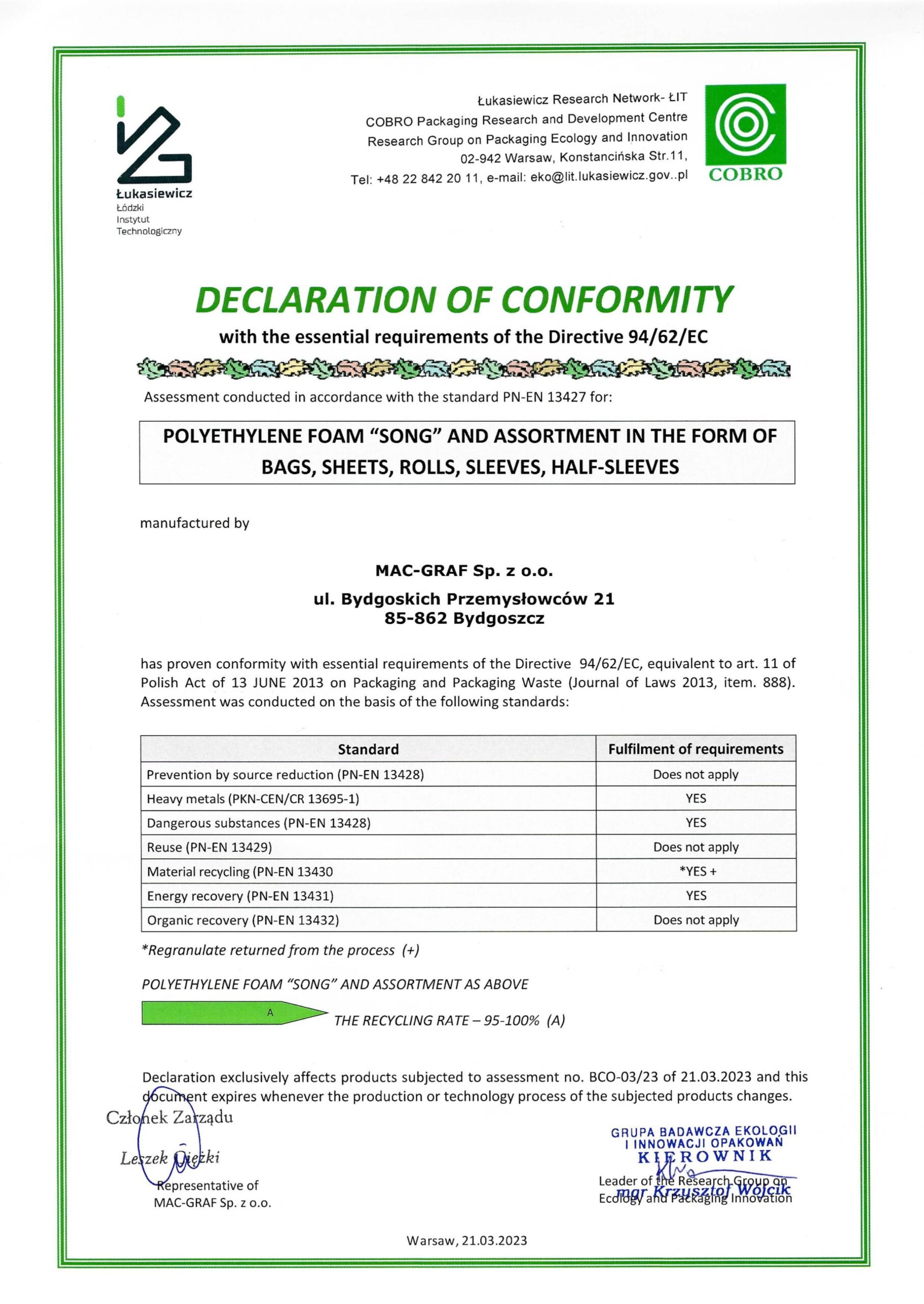
Case 2 | Replacing a standard product with a dedicated product
Our clients often use polyethylene foam from a roll for packaging, which is cut by warehouse workers. However, some of them switched from this solution to ready-made sheets with pre-determined dimensions, thanks to which the stage of cutting the foam was eliminated from the packaging process. An additional advantage is the control over material consumption – it does not depend on the decision of the employee who can cut the foam from the roll to different widths.
At Mac-Graf we offer PE foam in widths tailored to the customer's needs. If it notices material losses because, for example, it buys 120 cm wide rolls and actually needs 110 cm for packaging, then in order not to cut off those 10 cm, it can order custom-made rolls from us – 110 cm wide. This decision means that there are no leftovers in the warehouse that need to be disposed of, the packaging time is shorter and the cost is lower because the price of the roll is then lower (the client actually pays for 110 cm and not 120 cm).
Case 3 | Product with a larger winding
Packing tapes are one of the most basic materials in every warehouse. Although their unit price is low, on a large scale of operation, a small change can generate significant savings on an annual basis. In the past, 66 m tapes were popular among our clients, then 60 m ones, and now we are implementing 100 m and 150 m tapes for many of them. Why? A longer roll means less waste and usually a lower price per meter. Additionally, tapes with a large roll need to be replaced in the feeder less often.
When optimizing for tapes, remember that a large coil will not always be the right solution. If packaging is done manually in your warehouse and you also employ women, a large coil and therefore a heavier tape may prove ineffective and cause injuries among female employees.
It is also worth analysing how wide the tape needs to be. Our client made a simple optimization and determined through testing that it could successfully use a narrower tape. In his case, it is sufficient to secure shipments and therefore uses less material.
The same principle regarding winding applies to other materials, e.g. PE foam or bubble wrap. When ordering a product with a larger roll, there is no need to change the roll in the feeder as often. Therefore, it is worth testing various solutions and analysing the working time of warehouse workers, because with larger scale shipments this small element can generate a significant difference in time and, consequently, in the cost of packaging.
We can help you and optimize the packaging process in your company
Do you want to verify whether your packaging process can be optimized by changing packaging materials or using appropriate tools?
Leave your contact details and our consultant will call you and discuss your needs and cooperation possibilities.
Make an appointment with our advisor
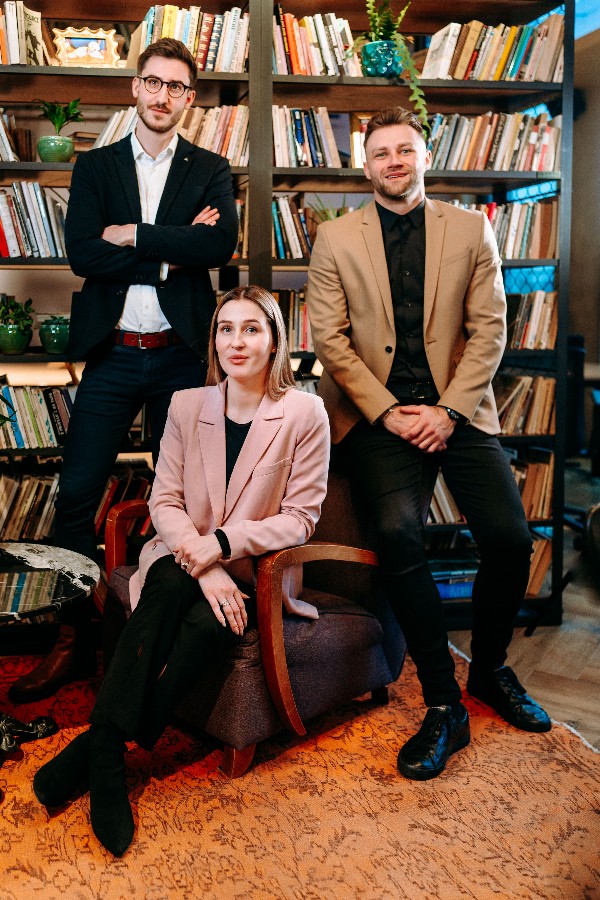